Problemi come questo furono una componente principale, fin dall’inizio, dell’interfaccia operativa sistematica tra il mondo industriale e coloro che costituiscono, al tempo stesso, i suoi arbitri e utilizzatori umani. Poiché nostra è la dicotomia tra l’ambizione e la condiscendenza, rispettivamente nei confronti di quanto è desiderabile ottenere in determinate circostanze, rispetto ai limiti fisici e mentali inerenti nel contesto tangibile dell’esistenza. E non vi è funzione maggiormente rilevante, di quella che collega il risultato perseguibile al margine d’errore latente. Prendiamo, per esempio, il caso della flangia: caratteristica strutturale di un tubo. Se non altra componente lineare di un impianto, che dovendosi trovare saldamente collocato saldamente in posizione, si troverà ad allargarsi perpendicolarmente in un disco finale; ragionevolmente traforato, ad intervalli regolari, da una serie di fori perfettamente tondi. E dentro di essi cosa mai potremmo prevedere prevedere, se non gli elementi che provvederanno a cementare l’ideale assemblaggio avvitandolo una serie plurima di volte, ancora e ancora, finche neanche in benché minimo refolo d’aria (per non parlar dell’acqua) possa uscire da una minima quanto indesiderabile fessura latente? Il che significa, signori, olio di gomito… Senz’altro, ma anche un certo grado di continuità e coerenza, come ebbe famosamente a rilevare l’impiegato del servizio idrico di New York J. H. Sharp nel 1931, frustrato dallo stringimento più che mai variabile, e purtroppo spesso insufficiente, nei diversi siti rilevanti della rete sotterranea urbana per la semplice ragione che anche utilizzando leve o moltiplicatori di forza, i nostri muscoli non sono stati concepiti per determinare in maniera scientifica quanto possa essere “abbastanza” in un contesto che fuoriesce largamente dalla nostra percezione naturale del mondo. Ecco qui che scaturì l’idea, destinata a un lungo seguito e processo evolutivo, della prima chiave dinamometrica manuale. Ovvero a quel tempo, nulla più che una chiave di manovra del tipo anglosassone (la tipica wrench) ma dotata di un complesso meccanismo di misurazione con deviazione della leva d’appoggio, per assegnare un numero alla resistenza del bullone di turno, indipendentemente dalla soggettiva percezione del suo utilizzatore. Il che poteva certamente funzionare, in una larga serie di contesti, ma che dire dell’evoluzione progressiva delle aspettative che potremmo al giorno d’oggi ricondurre ad una simile esigenza? Pensate a tal proposito al fissaggio di un albero di trasmissione tubolare di una centrale idroelettrica, di un grande motore navale o agli elementi strutturali di ponte sospeso. Tutte situazioni in cui la scala della forza necessaria, assieme alla sua precisione in fase di montaggio, si trovano semplicemente ad una scala largamente al di sopra dalle cognizioni precedenti. Ed è qui che l’energia muscolare umana, sostanzialmente, esce totalmente fuori dal quadro in essere. Lasciando il posto a tre diversi approcci: un pistone, la pressione, il calore interno. Ciascuno corrispondente ad una particolare tipologia di strumenti.
Cominciamo dunque il nostro elenco dall’attrezzo noto come chiave a torsione, che forse il più diffuso, ma non necessariamente versatile, dei tre approcci che andremo a citare. Quello consistente nell’impiego di un meccanismo a cassetta, ovvero finalizzato a ricoprire e circondare il bullone, coadiuvato da un raccordo corrispondente esattamente alla misura del componente, necessariamente collegato a due tubi di raccordo per l’immissione, a seconda dei casi, di fluido idraulico o aria ad altissima pressione. Tutto questo al fine d’indurre il moto in un cilindro dotato di una camma, che pur facendo avanti e indietro, può soltanto spingere innanzi l’ingranaggio esterno alla brugola, così da stringere (o allargare) il bullone. Simili strumenti, d’altra parte, devono per forza essere voltati dall’altra parte, nel caso in cui si debba stringere piuttosto che allargare, o viceversa…
Nota: nel video di apertura potete osservare un tipo di chiave a torsione particolarmente evoluto ed introdotta sul mercato soltanto a partire dal 2014, in cui il sistema regolabile del braccio di reazione (normalmente poggiato ad un bullone vicino o altra parte della flangia per impedire la rotazione dell’intero attrezzo) è stato sostituito da un ingegnoso pignone simile a una rondella, destinato a rimanere permanentemente dopo il montaggio del bullone. Ciò permette alla chiave di operare senza creare pericolosi punti di pressione, in cui schiacciare potenzialmente dita o mani dell’utilizzatore.
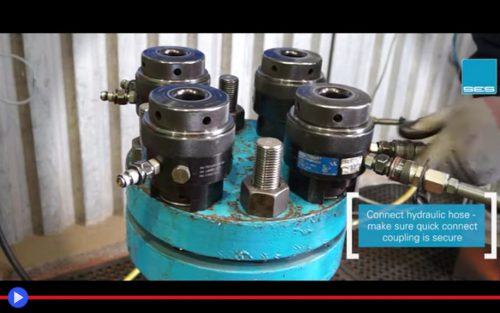
La necessità di operare all’interno di situazioni delicate come sott’acqua o in fabbriche o stabilimenti chimici, d’altra parte, ha reso non sempre applicabile il sistema basato su un approccio meccanico tanto complesso. Questa è d’altra parte la natura stessa degli standard di sicurezza, che non possono in alcun modo basarsi sulla probabilità, quanto l’ancorché remota evenienza che un qualcosa possa finire per andare storto. Ed è forse proprio in osservanza della proverbiale legge di Murphy, che è oggi possibile constatare l’esistenza di un sistema alternativo per raggiungere lo stesso scopo, convenzionalmente definito il tensionamento idraulico mediante l’impiego dell’eponimo attrezzo. Siamo qui di fronte ad un sistema per aggiungere pressione al punto di raccordo che potremmo definire particolarmente strategico, poiché piuttosto che applicare direttamente la forza necessaria, modifica intelligentemente la soluzione in essere, semplificando in modo significativo un passaggio tanto delicato e complesso. Siamo dunque, ancora una volta, innanzi ad un cappuccio che ricopre e incapsula totalmente la testa del bullone, sebbene questa volta sia di un tipo ancora più ingombrante, proprio perché necessariamente in grado di creare il vuoto all’interno. O in alternativa, immettere una grande quantità di fluido, la maggiore immaginabile e poi proseguire a farlo, con palese spietatezza nei confronti di componentistica creata per resistere all’impossibile. Ottenendo l’inimmaginabile: ciò in quanto il cappuccio in questione, stretto tramite l’impiego di un piolo (anche detto tommy bar) inserito a turno nell’apposita serie di fori, si trova saldamente avvitato nella parte finale della vite, successivamente al bullone sottostante. Il che significa che maggiore è il fluido idraulico pompato nello spazio stagno, più la pressione sulla vite in questione continua ad aumentare, estendendo come una sorta di possente molla l’acciaio di cui è composta. Approccio a cui fa seguito l’inserimento dello stesso piolo nei fori precedentemente previsti nel componente inferiore della macchina posizionato sul bullone, grazie all’apertura laterale sull’involucro esterno. Affinché al deflusso dell’olio di lavorazione, la vite torni rapidamente alle dimensioni e specifiche di partenza. Assicurando una chiusura inopinabile ed incomparabile di qualsivoglia tipologia di flangia (per non parlare della misurabilità della forza, rilevabile mediante una tabella della pressione raggiunta all’interno).
E che dire invece di coloro che trovandosi ad affrontare l’irrealizzabile, decidono piuttosto di accorciare le distanze, ovvero aggirare totalmente la questione in grado di complicargli l’esistenza? In uno specifico momento pregresso, fu dunque osservato come oltre l’80% della forza necessaria allo stringimento di un bullone derivasse dall’attrito tra scanalatura della vite e filetto, ovvero il proverbiale maschio e femmina di un simile punto d’incontro. Per cui fu chiaramente desumibile come una possibile soluzione al problema potesse derivare, ancora una volta, dal mero riscaldamento dell’ambiente… Interno. Sto parlando, per usare terminologia più chiara, del riscaldamento a induzione, il terzo e forse più surreale dei metodi impiegati per lo stringimento del bullone gigante. Facilmente riconoscibile, anche ad anni ed anni dal miracolo compiuto, dalla presenza nella vite stessa di un vistoso foro centrale, che sembra proseguire fino alle viscere del meccanismo. Immaginate, a tal proposito, un massiccio blocco di metallo, e il poco effetto sulla sua solidità strutturale che potrebbe derivare da un siffatto spazio vuoto. Cosa potrebbe mai impedirci, a questo punto, d’inserire una barra termica all’interno, tale da poter raggiungere agevolmente una temperatura tra i 150 e 200 gradi centigradi? Non poi così elevata, nello schema generale delle cose. Ne mantenuta sufficientemente a lungo da raggiungere l’esterno del bullone stesso; così che alla conseguente dilatazione del reticolo metallico del componente, esso potrà letteralmente esser fatto girare a mano libera: notevole, nevvero? Non sto affatto scherzando. Se per caso voleste sentirvi per un giorno simili all’Incredibile Hulk, il mio consiglio è quello d’impiegare almeno una volta nella vita la tecnologia del riscaldamento a induzione. Il che tende a prevedere una certa tipologia di carriera e scelte di vita…
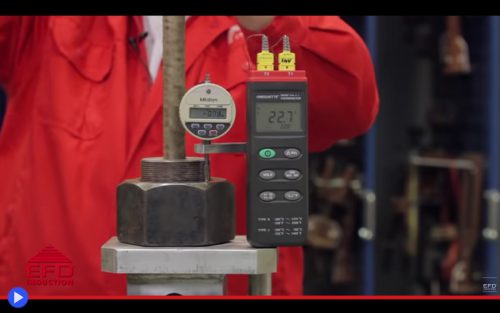
Circondati in ogni attimo dalle salienti realizzazioni dell’ingegneria contemporanea, siamo spesso inclini a mantenere il nostro sguardo verso l’orizzonte di una qualche aleatoria realizzazione futura. Non sempre ricordando, per trascuratezza o mera convergenza dei rapporti logici tra gli elementi, l’alto numero di soluzioni, i molti anni di lavoro e cognizioni, gli approcci fallimentari lasciati addietro nel tortuoso avanzamento del progresso. Che in quanto tale, sembra spesso assomigliare maggiormente a un fiume, piuttosto che una pratica strada asfaltata che si annulla nel punto di fuga.
E perciò non può che trovarsi a trarre giovamento, in determinate circostanze, dalla guida e la supervisione di opportune dighe ed argini costruiti dall’umana civilizzazione. E chi potrebbe immaginare simili strutture, senza almeno l’ombra persistente e alquanto inamovibile di una flangia!