Non più soltanto Pippo e Paperino. Dai laboratori della Disney Research di Zurigo, divisione tecnologica del grande colosso dell’intrattenimento associata al politecnico del capoluogo del cantone omonimo, provengono ogni anno alcune significative invenzioni dalle evidenti potenzialità commerciali, che tuttavia sono così distanti dal quotidiano, e di avveniristica concezione, da ritrovarsi tranquillamente associabili al mondo della scienza pura. Robot che camminano sui muri, algoritmi semplificati per il movimento della stoffa, sistemi virtuali per il calcolo dei castelli di sabbia, approcci alternativi per animare le marionette… Tutto questo presentato al pubblico, spesso durante prestigiose fiere internazionali della tecnologia, con un’assoluto candore e completezza, senza porsi il problema di proteggere la propria proprietà intellettuale, con finalità difficilmente associabili alla mera generazione di un profitto. Eventi come il SIGGRAPH (Special Interest Group on GRAPHics and Interactive Techniques) la cui edizione estiva del 2016 si è appena conclusa presso la città di Anaheim, nell’Orange County californiana, e per la quale Disney ha nuovamente presentato una proposta che si colloca nel campo tanto spesso rivisitato della stampa tridimensionale. Si tratta, essenzialmente, della risposta alla seguente domanda: sarebbe possibile, per un hobbista, una piccola azienda o un dipartimento universitario, creare con semplicità un quantità variabile di oggetti, dalla forma altamente specifica e per di più, in technicolor? Fino ad oggi, la risposta sarebbe stato un chiaro ed immediato “no”. Perché anche con l’attuale semplificazione intercorsa del processo per creare dei prodotti a partire dall’estrusione e/o deposizione della plastica, successivamente al raffreddamento di quest’ultima non è possibile che prevedere una seguente procedura per limare, togliere le parti in eccedenza e quindi, solo successivamente, applicarsi di buona lena con le proprie vernici d’ordinanza. Non per niente, uno degli ambiti in cui l’impiego di simili macchinari ha colpito maggiormente il grande pubblico è la realizzazione di miniature per i giochi da tavolo, per le quali è già previsto, è viene considerato addirittura desiderabile, l’uso diretto del pennello da parte dell’utente finale. Ma un conto è fare le cose per scelta, ed un altro perché non ci sono alternative. Ed una valida soluzione, per chi forse la stava ancora cercando, eccola finalmente qui per noi. Si chiama computational thermoforming, ed ha MOLTO a che vedere con la realizzazione della grafica per film e videogiochi.
È una visione affascinante, che molti siti e blog hanno già definito “magica” per probabile associazione con l’aggettivo che da sempre Disney ama attribuirsi nelle sue campagne di marketing o nel branding ufficiale. Sarebbe del resto difficile negargli simili prerogative, per lo meno in questo specifico, rivoluzionario caso. Su quella che parrebbe essere una scatola di metallo, è posta una stampa di forma pressoché quadrata raffigurante in 2D i soggetti più diversi: un ceppo di legno, un pezzo di pane, la carrozzeria di un’automobilina, la maschera del teatro cinese che raffigura il generale Wei Qi Gong, nume tutelare delle abitazioni. Quindi l’operatore preme un tasto fuori dall’inquadratura, e le immagini sembrano all’improvviso prendere vita, sollevandosi verso l’alto in una ragionevole approssimazione della forma reale di ciò che stavano rappresentando. E non è finita qui: uno sbuffo d’aria, un brusco suono, e subito dopo l’estrusione rientra in parte, aderendo in modo puntuale alla perfetta forma che palesemente era desiderabile allo scopo. Tutto è perfetto e pienamente allineato, la forma con l’immagine, il profilo con la sua profondità. Manca soltanto di chiarire come, effettivamente, un simile fenomeno possa essersi compiuto sotto i nostri spalancati occhi?!
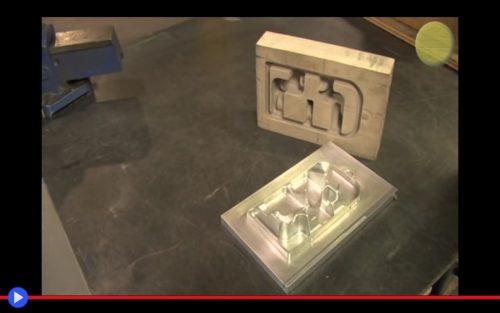
Come in ogni innovazione tecnologica che si rispetti, nulla nel procedimento può essere considerato totalmente nuovo. Ad iniziare dal concetto stesso, che si chiama termoformatura. E costituisce uno degli originali metodi per plasmare la plastica assieme allo stampaggio ad iniezione, essendo stato usato negli anni per gli scopi e nei campi industriali più diversi, con un occhio di riguardo al packaging alimentare, alla produzione di piatti e bicchieri di carta e persino alla realizzazione dell’interno di automobili, frigoriferi ed altri elettrodomestici presenti nelle nostre case. Ciò che caratterizza principalmente questa metodologia, e la distingue dall’alternativa succitata, risulta dunque essere l’approccio per porre a contatto il materiale con lo stampo. Che mentre nel caso dell’iniezione, è chiuso da ogni lato e viene letteralmente colmato, grazie all’uso di sistemi a pressione, qui entra in contatto solamente da un lato, quello inferiore per l’appunto, tramite l’elevazione di un piano mobile del tutto affine a quello usato dalla Disney nella sua dimostrazione. Stampo che dovrà essere, ovviamente, resistente al calore, poiché l’impiego di temperature elevate è l’unico sistema per rendere malleabile la plastica, consentendogli di adattarsi alla forma dell’oggetto desiderato. Ed è proprio qui, che troviamo la prima modifica al processo tradizionale: poiché in ambito industriale, dove i volumi di produzione sono necessariamente ingenti, il modo più pratico per creare la forma consiste nella lavorazione in CNC di un singolo blocco di alluminio, con dispendio relativamente elevato ed un’inevitabile surplus di materiali. Mente il team di ricercatori coinvolti nel progetto del computational thermoforming, composto da Christian Schuller, Daniele Panozzo, Anselm Grundhofer, Henning Zimmer, Evgeni Sorkine e Olga Sorkine-Hornung, ha ben pensato di ricorrere a una soluzione più pratica ed immediata: la realizzazione, tramite il processo di stampa tridimensionale, un negativo in plastica, all’interno del quale hanno quindi versato una resina auto-indurente dalle notevoli doti termiche, il gypsum. A seccatura avvenuta, quindi, hanno usato una fiamma viva per rimuovere la parte non necessaria, ottenendo una perfetta versione solida, naturalmente ancora monocromatica, di ciascun prodotto finale. La quale, salendo dal basso, dovrà occuparsi di piegare conseguentemente una lastra di plastica perfettamente allineata e pre-riscaldata fin quasi allo squagliamento, sulla quale era stata precedentemente stampata a colori l’immagine, o texture che dir si voglia, desiderata sul prodotto finito. Quindi, con l’aspettativa di stupire il mondo intero, i ricercatori hanno messo a frutto i risultati di un accorgimento MOLTO particolare…
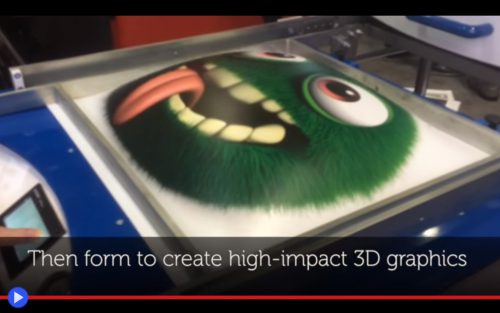
Che era stato messo in atto fin da subito, durante il processo di stampa dell’immagine da trasferire sulla plastica di lavorazione. Tutto ha origine, nemmeno a dirlo, nelle regioni virtualizzate ed iperboree della più pura scienza informatica: ed è per questo che ho citato, poco più sopra, due dei campi in cui si trova più spesso applicata la grafica 3D, film e videogiochi. Mentre qui si tratta, essenzialmente, di un sistema specifico per l’allineamento della stampa in due dimensioni alla forma dell’oggetto desiderato, grazie all’interfacciamento tra le macchine e un sistema simula l’effettivo processo di realizzazione, dando all’operatore una chiara idea di quanto fuoriuscirà, in effetti alla fine, dalle profondità del suo apparato termico estrusivo. Il procedimento necessario alla finalizzazione dell’opera diventa, quindi, molto simile a quello di chi si stesse applicando la texture su modelli tridimensionali virtualizzati, con software di largo uso nell’industria, quali 3D Studio o Maya, con la sola (significativa) differenza che il frutto della propria mente e mouse, alla fine, potrà essere toccato con mano. Ed il tutto tramite l’utilizzo di macchine assolutamente già disponibili sul mercato, tanto che l’unica effettiva “magia” presente nell’intera procedura è alla fine quella puramente intangibile, del software di calcolo che effettua l’allineamento della grafica col pezzo in materiale plastico fatto e finito. Il che significa, se vogliamo, che qui non c’era fin da principio nulla da vendere al grande pubblico, se non l’idea. Un qualcosa che difficilmente avrebbe reso dei profitti validi per un colosso come la Disney, che di certo non ha grandi interessi a muoversi nell’ambito dell’interscambio tra le aziende, ma cerca la sua fortuna esclusivamente dal rapporto diretto col cliente finale.
Ed è proprio questo, in ultima analisi, l’aspetto maggiormente significativo di divisioni come quella di Zurigo, che non hanno la missione chiaramente definita di far profitti subito e di continuo, ma piuttosto possono perseguire le proprie finalità di ricerca ad ampio spettro, aspettando d’imbattersi, prima o poi, in qualcosa di assolutamente rivoluzionario. Quello si, degno di essere custodito in cassaforte! Ma sulla strada per il quale, è semplicemente indispensabile visitare ogni regione dell’umana creatività. Difficile immaginare una posizione più soddisfacente, e formativa, per un entusiastico neo-laureato in ingegneria…